GMA/SSA
AI agents that think, explain, and scale expert knowledge
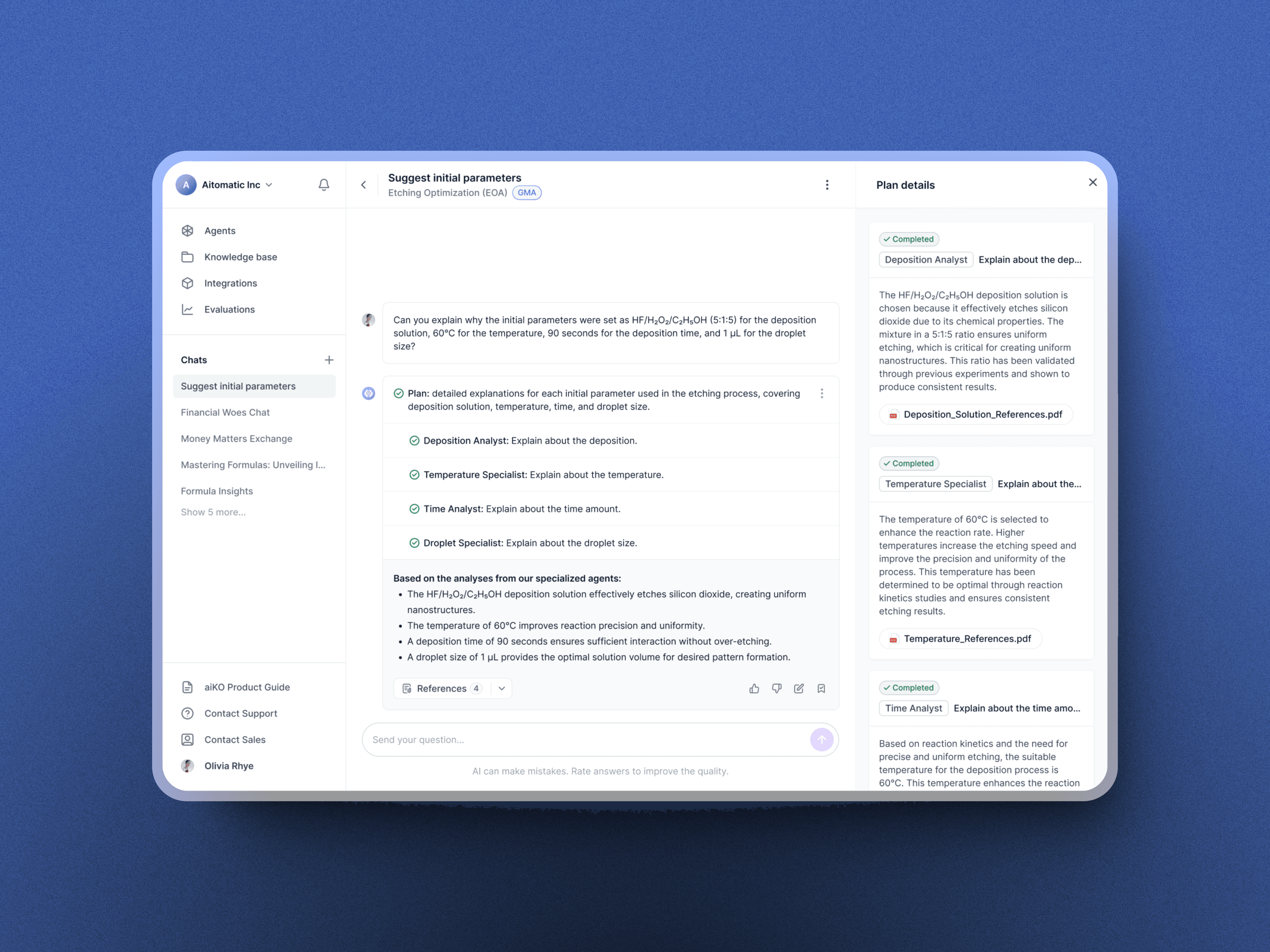
Problem
Tokyo Electron Limited faced a challenge in semiconductor etching: every cycle depended on trial and error, risking massive inefficiencies in one of the most precision-driven industries in the world.
Solution
I led the product vision and execution for GMA/SSA, an AI-powered system that eliminated guesswork, restructured workflows, and created a self-learning knowledge base for optimization.
Setup time dropped by 30%, for faster production.
Each etching cycle saved $20K on average.
Company
Aitomatic
Position
Head of Product & Design
Year
2024
Market
APAC & US, B2B
Context
Semiconductor manufacturing demands absolute precision.
At Tokyo Electron Limited, Process engineers with nearly a decade of experience were manually adjusting hundreds of parameters (gas mixtures, droplet sizing, plasma power, temperature) through trial-and-error cycles. Miscalculations cost tens of thousands per wafer, introducing production delays despite fragmented knowledge trapped in emails and personal notes.
When TEL approached us at Aitomatic, they didn’t just need an AI tool but an entirely new way of making decisions: repeatable, transparent, and scalable. My role was to lead the product vision and redesign TEL’s decision-making workflows around explainable, human-centered AI.
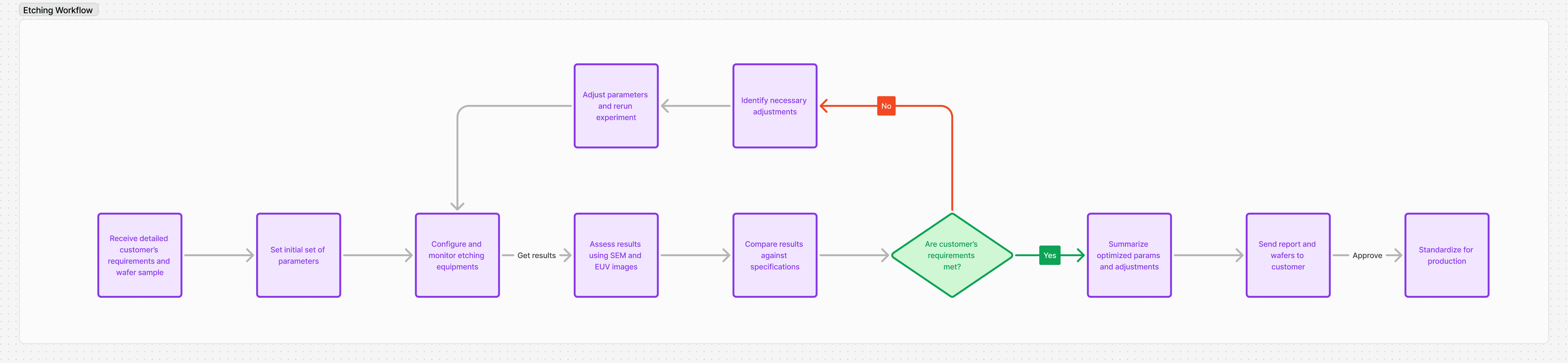
Challenges
The core challenge was decision opacity.
Engineers routinely re-solved the same problems in isolation. Workflows were inconsistent, results varied wildly between facilities, and every cycle was a high-stakes guess. Past attempts to integrate AI had failed because they lacked trust.
What TEL demanded wasn’t automation but AI that could reason, learn, and communicate with the fluency of a domain expert.
Design principles
I anchored the solution around three core design principles:
AI had to speak the language of the expert, not just make recommendations, but explain why, clearly and contextually.
Engineers needed visibility and control. AI would be a collaborator, working alongside them, not above them.
Intelligence had to become infrastructure. The system needed to retain and scale institutional memory across sites and shifts. Every decision had to enrich the system for the next.
Design process
To translate those principles into action, I led the contextual research: talking with TEL process engineers, dissecting their workflows, surfacing pain points, and mapping the true anatomy of decision-making in etching.
From this, I facilitated collaborative design sprints that brought together TEL’s domain experts with our AI teams. Together, we built rapid prototypes that clarified the deeper logic of how agentic reasoning should unfold inside the product.
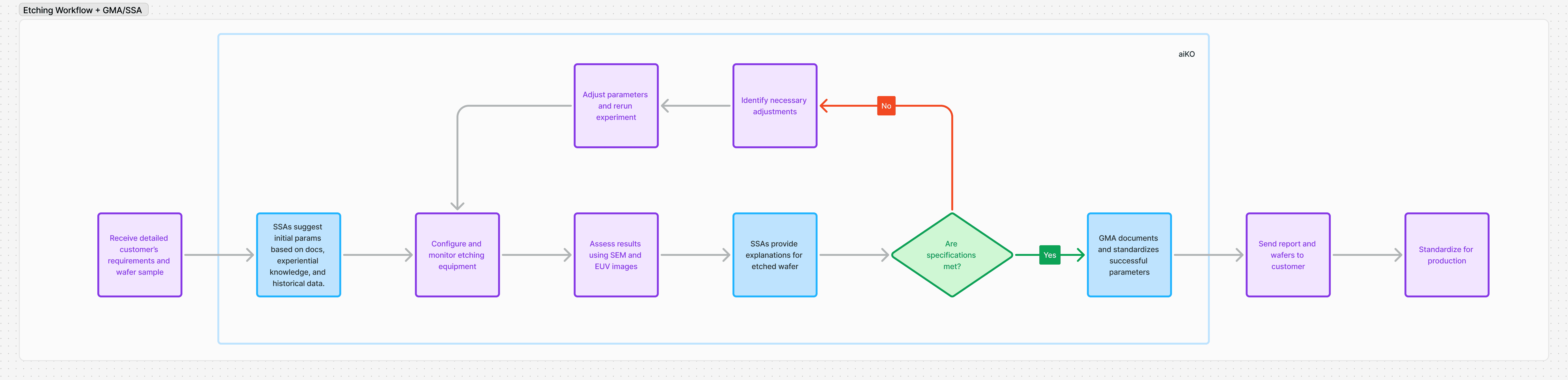
What we built
We developed the GMA/SSA system, a multi-agent AI network structured specifically around TEL’s complex workflows:
GMA (General Management Agent): Coordinated overall workflow, task logic, and synthesizing final recommendations.
SSAs (Small Specialized Agents): Domain-specific experts for tasks like deposition analysis, temperature control, droplet sizing, and parameter timing. Each SSA clearly justified its recommendations.
Every successful parameter set became part of a live knowledge base, accessible across TEL’s global fabs. The process engineers could manage plans, choose agents, define logic (parallel or serial processes), and even retrigger workflows if initial results needed refinement.
If an SSA lacked knowledge, the system allows engineers to contribute missing infor. Over time, GMA/SSA grew smarter, learning continuously from the human expert input.
Impact
Before GMA/SSA, TEL’s optimization decisions were expensive and isolated guesses. After, they became precise, repeatable, and scalable.
Setup and optimization time dropped by 30%, increasing throughput. Each wafer cycle saved around $20K, and with over 500 cycles annually, the system might unlock over $10M. Process variability fell by 15%, creating predictable, repeatable results across fabs.
More importantly, engineers described GMA/SSA as “an expert who never forgets, always explains, and improves every time you use it.”